Aluminized Steel
Aluminized Steel products are for a host of end-use applications. Aluminized Steel is carbon steel coated, through the hot-dip process, with an aluminum-silicon alloy. This process assures a tight metallurgical bond between the steel sheet and its aluminum coating, producing material with a unique combination of properties as compared to steel or aluminum alone.
Aluminized Steel can be made using a variety of processes, but the most effective process is hot dipping. The process of hot dipping starts by cleaning the steel, placing it in a bath of aluminum and silicone (Type 1) or aluminum only (Type 2), and then removing it, allowing the coated steel to air dry
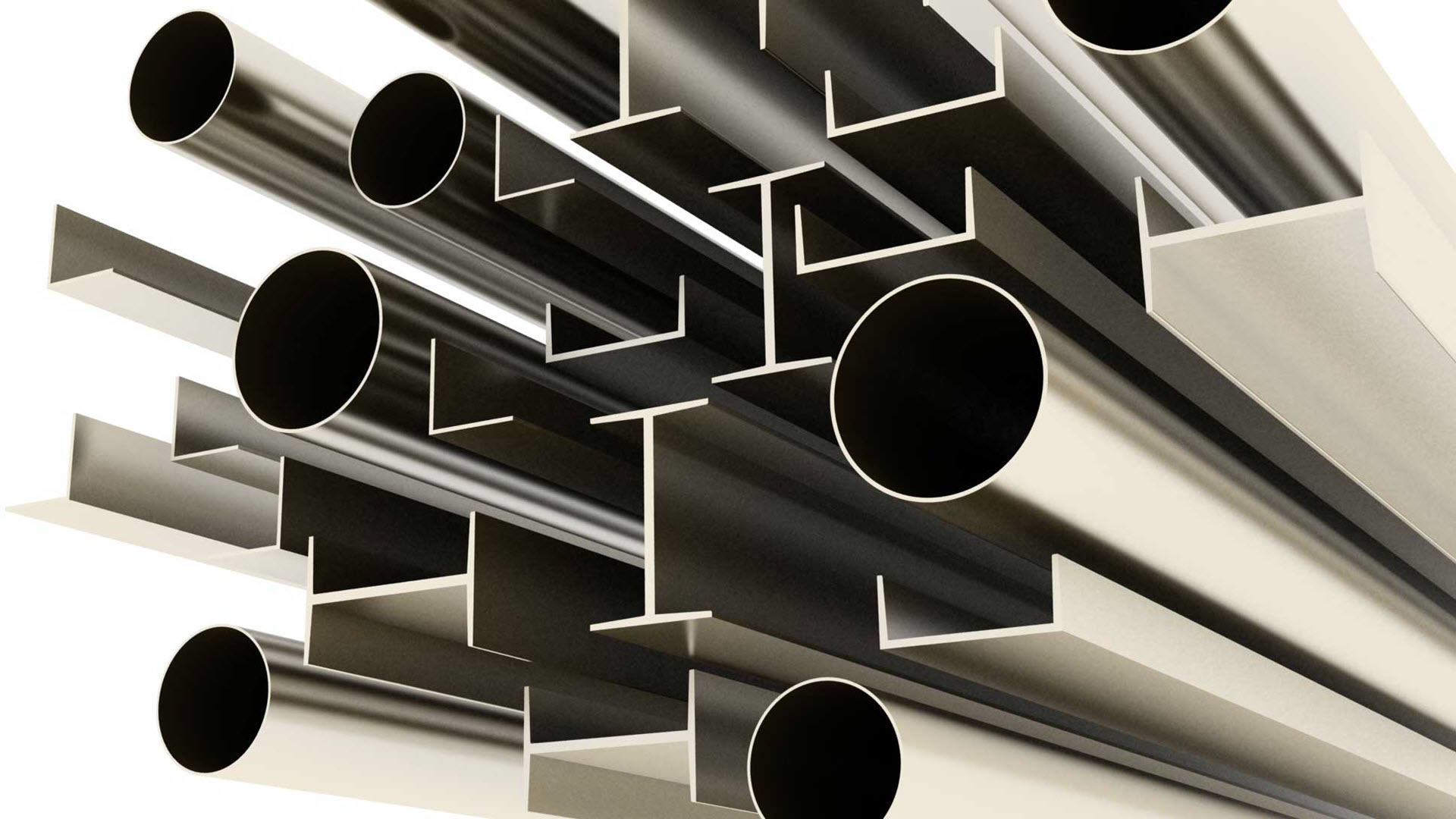
Type 1 and Type 2 Aluminized Steels can be used interchangeably in most applications. Cascadia Metals supplies Type 1 Aluminized Steel which contains approximately 90% aluminum and 10% silicon.
Benifits
Improved Yield Strength & Structural Durability
Maintains the strength of high alloy steel yet can be easily stamped, broken and bent to take on a wide variety of forms.- Corrosion Resistance
(Type 1) is highly resistant to corrosion because of the thin layers of aluminum and silicon, which keep the underlying steel from oxidizing. These thin layers also keep pit corrosion from occurring, especially during exposure to salts that affect most other metals. - Lower Cost
Cheaper to produce than high-alloy steels, such as stainless steel, and thus is a preferred material for manufacturing certain end-use products where heat and/or corrosion are a concern. Heat Resistance
Intended principally for heat resisting applications and also for uses where corrosion resistance and heat are involved. Formed to withstand 1,022 °F / 550 °C with almost no change in the base material.- Heat Transfer & Reflectivity
This Steel has a greater electrostatic surface than other metals which equates to better heat reflectivity. At temperatures up to 1,548 °F / 842 °C, and reflects up to 80% of heat projected onto it while maintaining its strength ASTM Specifications
ASTM Designation A463 outlines the general requirements for Aluminized Steel. Included in this specification are steel chemistry requirements, typical mechanical properties of various metallurgical grades, and the coating weight requirements for the different coating designations.Coating Thickness
Coating thickness is measured as the coating weight in ounces per square foot. For example, a coating designation of T1-25 specifies there is a minimum coating weight of 0.25 ounces per square foot on both sides of the sheet. The most common coating thicknesses are T1-13, T1-25 and T1-40.
Benifits
Improved Yield Strength & Structural Durability
Maintains the strength of high alloy steel yet can be easily stamped, broken and bent to take on a wide variety of forms.- Corrosion Resistance
(Type 1) is highly resistant to corrosion because of the thin layers of aluminum and silicon, which keep the underlying steel from oxidizing. These thin layers also keep pit corrosion from occurring, especially during exposure to salts that affect most other metals. - Lower Cost
Cheaper to produce than high-alloy steels, such as stainless steel, and thus is a preferred material for manufacturing certain end-use products where heat and/or corrosion are a concern. Heat Resistance
Intended principally for heat resisting applications and also for uses where corrosion resistance and heat are involved. Formed to withstand 1,022 °F / 550 °C with almost no change in the base material.- Heat Transfer & Reflectivity
This Steel has a greater electrostatic surface than other metals which equates to better heat reflectivity. At temperatures up to 1,548 °F / 842 °C, and reflects up to 80% of heat projected onto it while maintaining its strength ASTM Specifications
ASTM Designation A463 outlines the general requirements for Aluminized Steel. Included in this specification are steel chemistry requirements, typical mechanical properties of various metallurgical grades, and the coating weight requirements for the different coating designations.Coating Thickness
Coating thickness is measured as the coating weight in ounces per square foot. For example, a coating designation of T1-25 specifies there is a minimum coating weight of 0.25 ounces per square foot on both sides of the sheet. The most common coating thicknesses are T1-13, T1-25 and T1-40.
Options
Chemical Treatment
A chemical surface treatment is available which consists of a thin, invisible, corrosion inhibiting, inorganic, chemical film applied on both sides of the metallic coated surface. This film is applied at the metallic coating line by dipping the steel strip into a solution of corrosion inhibiting chemicals. The chemically treated surface is much more resistant to staining that typically occurs in humid conditions during storage or transportation.
End-Use Applications
Aluminized Steel, due to its inherent benefits, is commonly used in manufacturing mufflers, fireplaces, incinerators, heat inductors as well as other applications where heat resistance is required. Other applications of Aluminized Steel include corrugated roofing and siding, grain bins, drying ovens, and air-conditioner condenser housings.
Trusted Partners
Armour Cladding is proud to have created several stable and long-term relationships with various partners to ensure we provide you with the greatest product and value possible.
Trusted Partners
Armour Cladding is proud to have created several stable and long-term relationships with various partners to ensure we provide you with the greatest product and value possible.